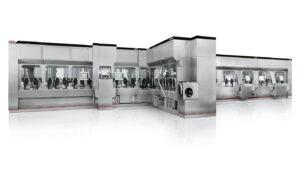
IMA protection and containment
The demands of safety, sterility assurance, and regulatory compliance are continuously increasing in pharmaceutical production.
By taking advantage of newest technology and combining it with traditional containment equipment, containment “gaps” can be minimised, and a more secure production process is reached. Moreover, it facilitates that protection and containment systems can be tailored to meet not only customer demands, but also FDA and EMEA regulatory guidelines.
PPS works together with IMA in delivering high quality protection and containment equipment.

IMA TWINVALVE High containment valve
No system can obtain the maximum Occupational Exposure Level without washing its valves. TWINVALVE combines IMA Active’s experience in powder handling and washing systems to ensure high containment.
The IMA TWINVALVE is a reliable solution to handle powders, granules, tablets and capsules in high containment.
This patented system can be used as a standard butterfly valve on bins and can be easily retrofitted on existing powder handling plants allowing containment during powder transfer.
- Simple design composed of two standard sanitary butterfly valves with an orbital rotating spray head.
- Different cleaning cycles allowed: cleaning by compressed air and cleaning by water/solvent.
- Drying phase by compressed air or steam performed at the end of the cleaning cycle.

IMA ISOLATION TECHNOLOGY Isolation solutions for aseptic fill finish lines
In the pharmaceutical sector the need to protect the product from contamination due to the presence of personnel or the environment is one of the major drivers for containment. What matters most in aseptic processes is the max. reduction of contamination risk.

IMA TWISTER Transfer system
Flexibility is the hallmark of IMA Active’s handling systems. Easily integrated with other equipment into solid dose processing lines, TWISTER allows product transfer in high containment.

IMA BARRIER TECHNOLOGY: OPEN & CLOSED RABS Barrier technologies for aseptic fill/finish lines
Open RABS represent the first solution available in the barrier technology scenario, introducing the concept of product protection.
Closed RABS provide minimal protection during manipulation of mildly potent products.
Open RABS is a simple solution, used extensively in the pharmaceutical sector, to separate the production area from the operator and the external environment. Product protection is only effective if the airflow is active, whereas no protection is offered to the operator when potent compounds are being processed. Easy to install and a cost-effective solution, it is the minimum barrier solution to be used in case of aseptic production environments.
Closed RABS is an evolution of the “Open” solution, providing a minimal degree of operator protection when potent compounds are being processed.
- Unidirectional Air Flow (UAF)
- Easy to validate (air flow, air classification, doors interlocks)
- Production area access control (doors can be interlocked)

IMA GS EVOLUTION Coating pan
Designed for highly automated installations, GS EVOLUTION represents the ideal base for a contained plant. The machine reduces operator exposure in case of the processing of high potent products.

IMA BLUE GALAXY Depyrogenating Tunnels
All pharmacopeia indicate Escherichia Coli type 5 as the endotoxin to be used for checking that a depyrogenation process is accomplished correctly. A depyrogenation process has to initially guarantee at least a log 3 reduction of endotoxins.
BLUE GALAXY is a series of depyrogenation tunnels designed to be incorporated in production lines that require continuous depyrogenation by means of dry heat. The wide range available responds adequately to any production requirement; top-level design technology allows use in any kind of application; easily integrated into lines handling highly toxic compounds or equipped with isolators.
- Completely automatic unloading procedure.
- The system for air balancing, pressurization and heating/cooling enables effective thermal treatment of glass containers.
- Control and automation system set-up with different PLC or PC types.
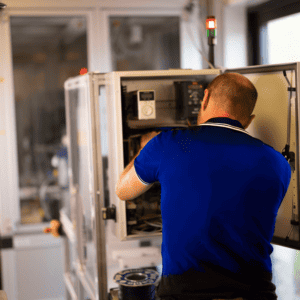
PPS Service & Aftersales
Uniquely for the industry PPS has its own service department, which is of great benefit to our customers. PPS service department has specially trained technicians with the highest expertise and experience. We offer a long list of services, including:
- Installation and renovation of existing equipment.
- Design of complete solutions; everything from the requirements specifications and logistics, to execution and validation.
- Competent feedback on automation solutions or other type of production optimization.
- Installing and/or moving entire production or packaging lines.
- Training of technical personnel and operators in optimal use of the installed equipment.
- Tailor-made service and aftersales agreements for ongoing maintenance as well as assistance in case of breakdown.
In addition, PPS delivers spare parts and consumables directly to our customers from own stock. Having our own stock ensures fast and efficient delivery, which minimizes any production downtime for our customers.
If you want to know more about our service department, please contact us directly or get more information here.